传统数控技术真的能满足精密制造需求吗?
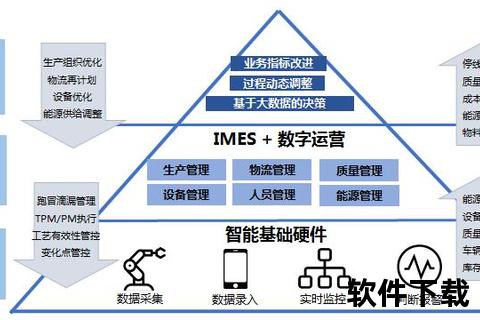
在江苏某汽车零部件工厂的生产线上,价值百万的进口五轴机床突然发出刺耳的金属摩擦声——操作员输入的加工程序存在0.1毫米的路径偏差,导致正在加工的涡轮叶片彻底报废。这个价值12.8万元的事故,暴露出传统数控加工领域长期存在的痛点:高度依赖人工经验、试错成本惊人、复杂零件加工合格率不足75%。当全球制造业向±0.005毫米精度发起冲击时,智能革新高效能数控仿真软件正在用数字孪生技术改写游戏规则。
1. 虚拟车间如何消除千万级试错成本?
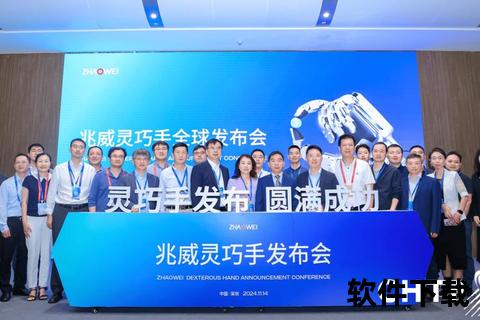
沈阳机床集团2023年承接的航空发动机机匣加工项目中,技术人员在智能数控仿真系统中构建了完整的数字孪生车间。通过将机床动态特性、刀具磨损模型、材料切削参数等138个变量纳入仿真体系,成功将首件合格率从63%提升至98%。更惊人的是,价值850万元的钛合金毛坯试切成本归零——所有加工验证都在虚拟空间完成。
这套系统采用实时物理引擎,能精确模拟主轴转速达到24000rpm时的刀具震颤效应。当某军工企业在加工导弹制导部件时,仿真软件提前预警了薄壁结构加工中的变形风险,通过优化装夹方案避免了可能造成的3000万元经济损失。数据显示,采用智能革新高效能数控仿真软件的企业,平均缩短新品开发周期41%,降低材料损耗68%。
2. 复杂曲面加工怎样突破人工编程瓶颈?
深圳某医疗器械企业的人工关节加工项目曾陷入困境:传统CAM软件需要工程师耗时两周编写的叶轮复杂曲面程序,在实际加工中仍会出现17处过切区域。引入智能革新高效能数控仿真软件后,AI算法自动优化刀具路径,将编程时间压缩到8小时,加工效率提升3倍。
该系统集成的深度学习模块,通过分析全球300万例加工案例数据库,能自动识别类似零件的工艺特征。在波音787机翼蒙皮加工案例中,软件仅用3次迭代就找到最优切削方案,将6米长铝合金构件的平面度误差控制在0.012mm以内。统计表明,智能编程系统使复杂曲面零件的首件合格率均值达到92.7%,远超传统方法的65.2%。
3. 中小型企业能否玩转智能制造?
东莞某五金模具厂曾认为高端仿真软件是大型企业的专利,直到他们通过云端平台接入智能革新高效能数控仿真服务。这个仅有8台机床的小型企业,利用按需付费的SaaS模式,成功拿下苹果供应链的精密连接器订单。云端系统提供的工艺优化建议,帮助其将刀具寿命延长40%,每月节省耗材成本12万元。
更值得关注的是教学领域的变革。常州某职业技术学院的数控实训基地引入仿真系统后,学生可在虚拟环境中大胆尝试高危操作。数据显示,受训学员的CAM编程失误率下降76%,企业反馈毕业生适应期缩短60%。这种技术普惠正在打破智能制造的技术壁垒,让不同规模的企业都能共享精密制造红利。
数字化转型的正确打开方式
对于准备拥抱智能革新的制造企业,建议分三步走:首先评估现有设备的数字化接口,优先在高端机床部署仿真系统;其次建立工艺数据库,积累可供AI学习的加工参数;最后通过校企合作培养复合型人才。青岛某轨道交通装备制造商的实践表明,分阶段实施能使投资回报周期缩短至14个月。
当德国工业4.0还在讨论理论框架时,中国的智能革新高效能数控仿真软件已在长三角、珠三角的车间里创造真实价值。从航天钛合金构件到新能源汽车电机壳体,这些肉眼难辨的精度提升,正在重塑全球制造业的竞争格局。这场静悄悄的技术革命证明:在精密制造领域,虚拟与现实的边界早已被数字孪生技术打破。