当传统制造业撞上材料浪费的"冰山",极致优化能否破局?
钢材价格连年攀升,制造业利润空间不断被压缩。国内某大型钢结构企业曾透露,每年因传统手工套料导致的材料浪费高达千万级。面对这块难啃的"硬骨头",老技工们凭经验排版的效率,真的敌得过人工智能算法吗?极致优化智能套料软件革新生产效能新境界 的诞生,正在改写这场博弈的结局。
1. 材料利用率能否突破人工极限?
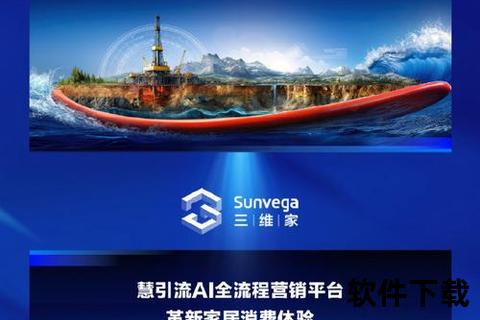
传统套料员排版时,零件间隙常留"安全余量",导致材料利用率普遍低于85%。而宁波某西装厂引入的智能套料系统,通过几何形状匹配算法,在异形布料上实现了96.7%的利用率。其奥秘在于三点:
智能嵌套引擎:如EZNest的"Part In Part"技术,可将小零件嵌入大零件孔洞,像俄罗斯套娃般利用每一寸空间
余料管理系统:上海某造船厂使用SigmaNEST后,将余料自动归档为"虚拟板材库",次年节省新板材采购费用380万元
动态填充策略:Radan软件通过混合整数规划算法,对1000+零件进行2000次排列组合模拟,找出最优解仅需5秒
2. 切割效率如何实现指数级跃升?
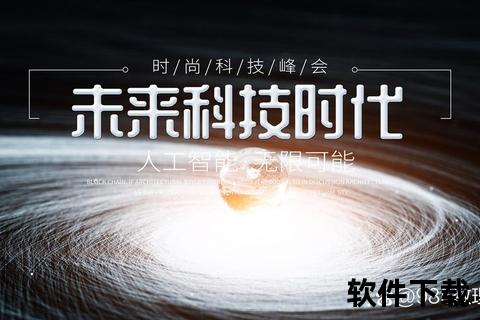
东莞五金加工厂曾因等离子切割机空跑率过高,月均损耗电极头达120个。部署极致优化智能套料软件革新生产效能新境界 后,三个关键升级带来质变:
共边切割技术:将相邻零件轮廓线合并,使切割路径缩短40%,某汽车配件厂单台设备日产量提升至1800件
智能桥接系统:InteGNPS自动在薄板零件间生成0.3-0.5mm微连接,防止变形的同时减少50%夹持次数
激光路径优化:Lantek的混合算法使切割头空程移动减少至人工排版的1/3,每年节省氩气消耗23吨
3. 生产管理怎样摆脱"数据孤岛"?
苏州某电梯部件制造商的痛点极具代表性:ERP里的板材库存总与实际相差20%,车间角落堆满"失踪余料"。智能套料软件的突破在于:
全流程数字化:从AutoCAD图纸直接生成带工艺参数的NC代码,消除人为转录错误
实时看板系统:重庆摩托车架生产企业通过云端看板,使计划部与车间数据同步延迟从4小时降至10秒
智能预警机制:某家电企业接入MES系统后,当材料利用率连续3次低于阈值时自动触发工艺评审
破局者的行动指南
要真正实现极致优化智能套料软件革新生产效能新境界,企业需三步走:
1. 选型适配:中小批量企业可选EZNest(年费8-15万),大批量生产推荐SigmaNEST(模块化订阅)
2. 人才培育:建立"算法工程师+老技师"的混编团队,某阀门厂通过双向培训使软件效用提升40%
3. 系统融合:优先选择支持RESTful API的软件,如Radan可与金蝶K3无缝对接,避免形成新数据孤岛
当切割路径开始用微米级精度跳舞,当钢板余料变成可追溯的数字资产,这场制造业的效率革命已悄然来临。选择观望还是拥抱变革,答案就在下一张智能排版图中。
--