当传统实验设计遭遇瓶颈,科研效率如何破局?
在科研领域,实验设计(DOE)是优化工艺、提升效率的核心工具。传统DOE方法长期面临两大痛点:耗时耗力与复杂交互难分析。例如,某食品企业曾因仅靠“单因素轮换法”优化工艺,导致实验重复上千次仍无法突破,最终损失百万级成本。类似的困境并非个例——如何用更少的实验次数、更精准的模型预测实现科研突破?答案正指向创新高效DOE软件赋能智能实验设计精准突破。
1. 传统实验效率低?算法驱动智能优化
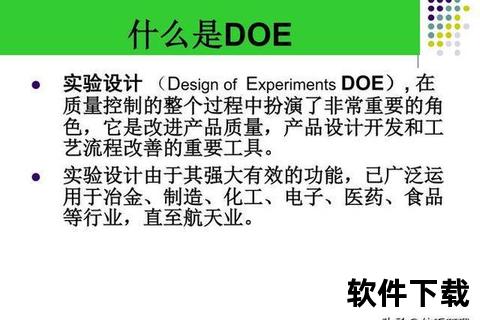
传统DOE依赖人工经验设计实验方案,但面对多变量、高维度的复杂问题,往往因实验次数过多而难以推进。例如,某生物医药团队在合成新药时,需同时调控温度、pH值、催化剂浓度等7个参数,若采用全因子设计需进行128次实验,耗时长达半年。
而新一代DOE软件通过机器学习与贝叶斯优化算法,将实验次数压缩90%以上。以创腾科技的iLabPower为例,其集成随机搜索和贝叶斯算法,能自动预测最佳参数组合区间。某材料团队利用该工具优化纳米材料合成工艺,仅用15组实验便锁定最优条件,产率提升23%,研发周期缩短至2周。类似的案例在化工领域同样显著:一项针对环丙沙星回收率的浊点提取实验,通过Design-Expert软件设计的27组实验,精准量化了Triton X-114浓度、温度等关键因素影响,预测误差低于5%。
算法优势:
随机搜索:快速覆盖参数空间,避免局部最优陷阱
贝叶斯优化:基于历史数据动态调整策略,提升预测精度
响应曲面建模:3D可视化参数交互效应,降低分析门槛
2. 多因素交互难解?动态建模打破数据孤岛
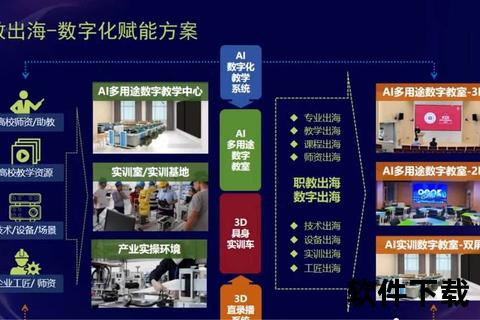
传统实验中,温度、压力、原料配比等参数常被孤立分析,而实际生产中这些因素往往存在非线互效应。例如,某汽车零部件厂商优化焊接工艺时发现,当温度与压力同时高于阈值时,焊缝强度骤降,但单独调整任一参数均无法发现此规律。
创新DOE软件通过多因素动态建模与数据融合,解决了这一难题。以Stat-Ease公司的Design-Expert为例,其响应曲面方法(RSM)能构建三维交互模型,直观展示参数间的协同或拮抗作用。某涂料企业利用该功能优化配方,发现固化剂浓度与搅拌速度的交互效应显著影响涂层硬度,最终通过调整两者比例,将产品合格率从78%提升至95%。
技术突破点:
数据双向关联:实验设计与记录无缝衔接,确保可追溯性
混合设计:支持工艺参数、配方成分与分类变量组合分析(如“烘焙温度+面粉比例+酵母种类”)
全局优化:基于EDBO算法平衡多个响应目标(如“成本最低+纯度最高+能耗最小”)
3. 跨行业需求差异大?模块化设计赋能全场景
从生物医药到材料化工,不同行业对DOE的需求差异显著。例如,药物研发需严格符合GMP规范,而材料合成更关注高通量实验能力。传统软件常因功能固化难以适配,但新一代工具通过模块化架构与行业模板解决了这一问题。
案例1:生物医药
美克家居在开发定制化家具涂料时,使用iLabPower的配方开发模块,将交付周期从120天压缩至35天。软件内置的“正交-均匀混合设计”模板,帮助团队快速筛选出6种环保添加剂的最佳配比,VOC排放降低40%。
案例2:智能制造
欧姆龙上海工厂采用LCIA系统,通过DOE软件实现生产线智能化改造。系统自动分析设备传感器数据,动态调整机器人动作参数,使一条产线可兼容22000种产品,故障率下降60%。
功能亮点:
预制模板:提供正交设计、田口方法等20+行业专属方案
云端协作:支持多团队并行实验,数据实时同步
合规性保障:符合FDA 21 CFR Part 11、GMP等法规审计要求
从理论到实践:科研人的行动指南
创新高效DOE软件赋能智能实验设计精准突破,但工具的价值取决于使用策略。基于行业实践,提出三点建议:
1. 按需选型:
材料/化工领域优先选择支持响应曲面和混料设计的工具(如Design-Expert)
生物医药团队可关注iLabPower等具备GMP合规性验证的软件
中小企业建议试用MINITAB等低成本工具,逐步培养DOE能力
2. 人机协同:
初期利用软件向导功能生成基础方案,再结合专家经验微调参数
建立“算法预测-小试验证-模型迭代”闭环,避免过度依赖自动化
3. 数据基建:
打通DOE软件与LIMS(实验室信息管理系统)、MES(制造执行系统)的数据接口
构建历史实验数据库,为机器学习提供高质量样本
正如统计学家乔治·博克斯所言:“所有模型都是错的,但有些是有用的。”在智能化浪潮中,DOE软件正从“替代人力”转向“增强智能”,而科研人的核心价值,在于将算法预测与领域知识深度融合,让每一次实验都成为精准突破的基石。
--