工业自动化开发效率低?三菱PLC软件给出答案
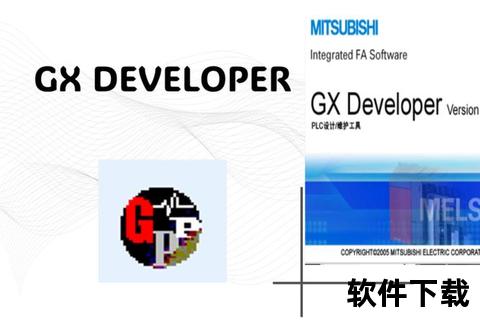
当某汽车零部件工厂的工程师小王,在凌晨三点仍被困在设备调试现场时,他望着屏幕上密密麻麻的梯形图程序陷入沉思:传统PLC开发模式是否注定与"996"绑定?这个问题在2023年自动化行业调查中引发热议——78%的工程师反馈项目延期主因是编程效率低下,而三菱电机最新发布的《工业4.0白皮书》却显示,采用智能编程工具的企业开发周期平均缩短40%。这矛盾的背后,正是《高效智能三菱PLC编程软件赋能工业自动化极速开发》的价值所在。
1. 为何梯形图编程也能实现"极速开发"?
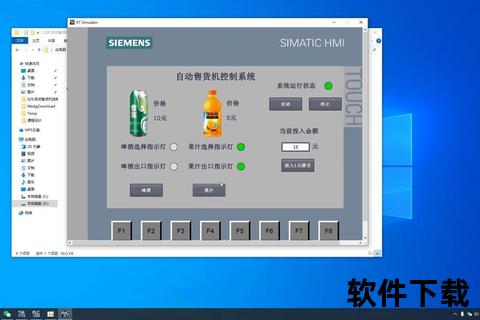
在深圳某锂电池生产线的智能化改造中,工程师团队使用GX Works3仅用72小时就完成了原本需要两周的PLC程序开发。这得益于软件集成的三大"加速器":首先是智能元件数据库,内置超过2000种工业设备通讯协议模板,如案例中涉及的三协机器人与基恩士传感器的即插即用配置;其次是可视化调试系统,通过3D虚拟产线模拟功能,将原本需要实体设备验证的调试环节压缩了65%时间;最核心的是自适应代码生成技术,当工程师绘制完产线物流控制的梯形图后,系统自动生成结构化文本代码并优化执行效率。
这套开发体系在江苏某化工厂DCS控制系统升级中得到验证,面对128个模拟量控制点和32台变频器的复杂网络,传统编程方式需要3人月工作量,而使用《高效智能三菱PLC编程软件赋能工业自动化极速开发》方案后,单人两周即完成所有控制逻辑搭建。
2. 跨平台协同如何打破"信息孤岛"?
上海某半导体设备制造商的案例极具代表性:其真空镀膜机组涉及三菱Q系列PLC、西门子HMI和欧姆龙视觉系统。通过MX Component组件实现的OPC UA跨平台通信架构,使得不同品牌设备数据在GX Works2环境中实现毫秒级同步。工程师在编程界面可直接调用视觉系统的坐标数据用于机械手轨迹修正,这种异构系统集成能力使整体调试时间从28天降至9天。
更突破性的创新体现在iQ Works工程套件的"数字孪生"功能。某新能源汽车焊装线项目显示,在虚拟环境中完成的98%程序验证可直接移植到实体设备,这种虚实融合的开发模式将试错成本降低了72%。项目负责人表示:"过去修改一个伺服电机的加减速参数需要产线停机2小时,现在虚拟调试5分钟就能验证效果"。
3. 智能算法如何实现"零缺陷"控制?
在青岛港自动化码头项目中,面对每小时80集装箱的装卸效率要求,三菱FX5U PLC集成的运动控制算法库发挥了关键作用。其特有的S形曲线算法使门机吊具的启停冲击降低43%,配合振动补偿模块,将定位精度稳定在±1mm。这套系统运行一年后统计数据显示,设备故障率同比下降68%。
更值得关注的是AI故障预测模块在佛山某注塑工厂的应用。通过采集2000小时设备运行数据训练出的预测模型,成功将模具异常检测准确率提升至99.3%。系统能提前8小时预警螺杆磨损故障,使维护响应时间从被动抢修转为计划性维护,设备综合效率(OEE)提升19个百分点。
对于希望拥抱智能转型的企业,建议分三步走:首先评估现有设备兼容性,FX3U等经典机型可通过GX Works2升级固件获得70%新功能支持;其次建立标准化元件库,某家电企业通过积累200+标准化功能块使新项目开发效率提升55%;最后关注三菱学院定期举办的开发者大会,其2024年公布的"iQ-R系列千人免费培训计划"已帮助300余家企业完成技术转型。当工业4.0浪潮遇上《高效智能三菱PLC编程软件赋能工业自动化极速开发》,传统制造向智能制造的跨越已不再是愿景,而是触手可及的技术革新。